TECHNICAL RESOURCES
DLS V2 - CENTERSTAGE 2023-2024

In approaching each design of our systems, we strictly follow an iterative engineering process that maximizes the chances of success by abstracting and analyzing weaknesses in detail in the virtual environment before prototyping. This strategy allows our team to consider many potential solutions for the season's mission without increasing the cost and production time. Thus, we were able to use more than 90% custom-made parts for our robots during the Centerstage season, allowing for greater creative freedom in our designs.
Through the advanced use of Solidworks Computer Aided Design software, the use of 4 3D printers and a CNC to manufacture the custom parts, the virtual simulation of the forces exerted on the systems, and the collaboration with university physics professors for the theoretical calculation of the efficiency and feasibility of the designs, the team managed to build two robots with the highest competitive aptitudes.
Extensive planning and research allowed us to arrive at reliable solutions for our robots while seeking low system complexity to eliminate the risk of failure during matches.
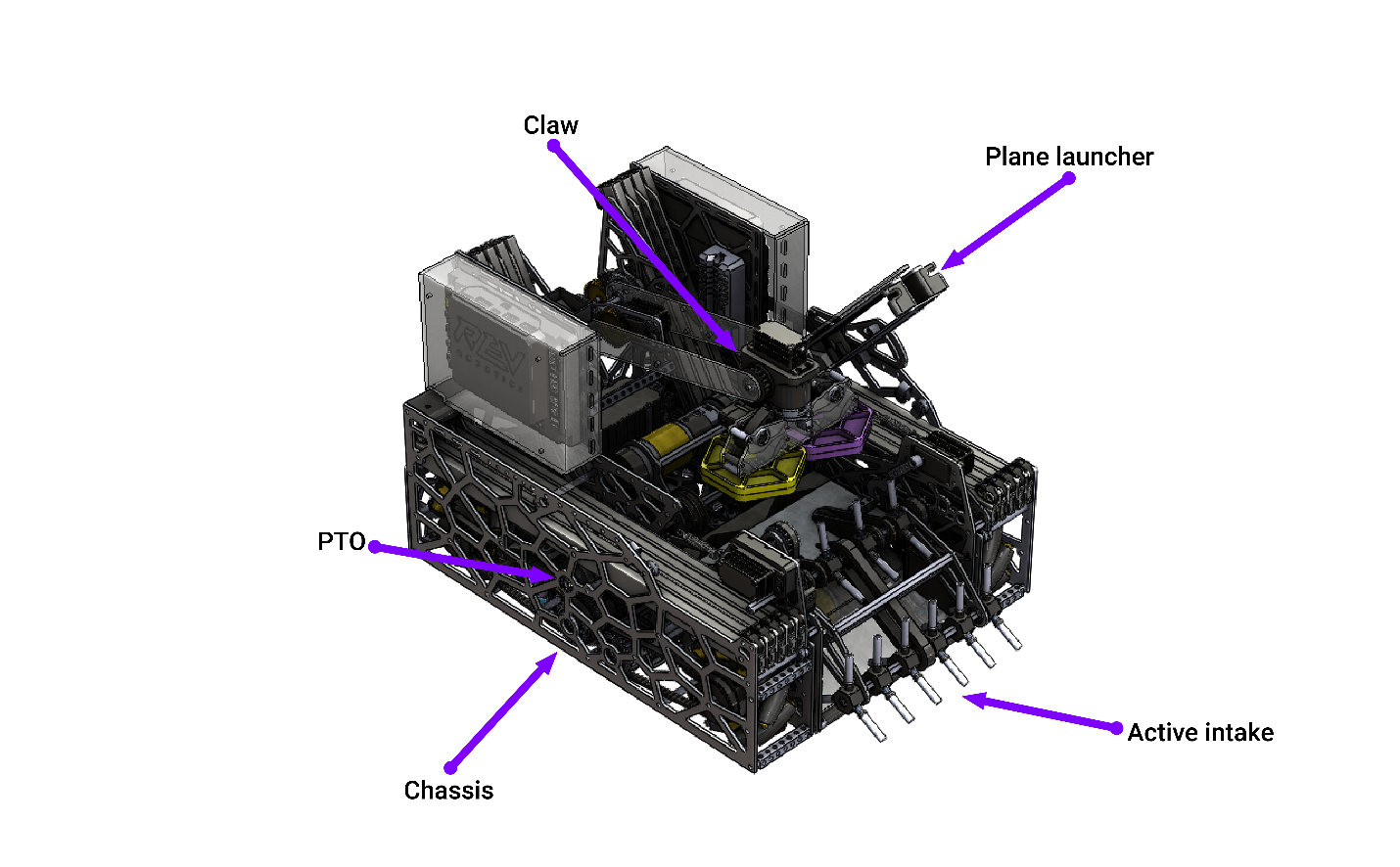
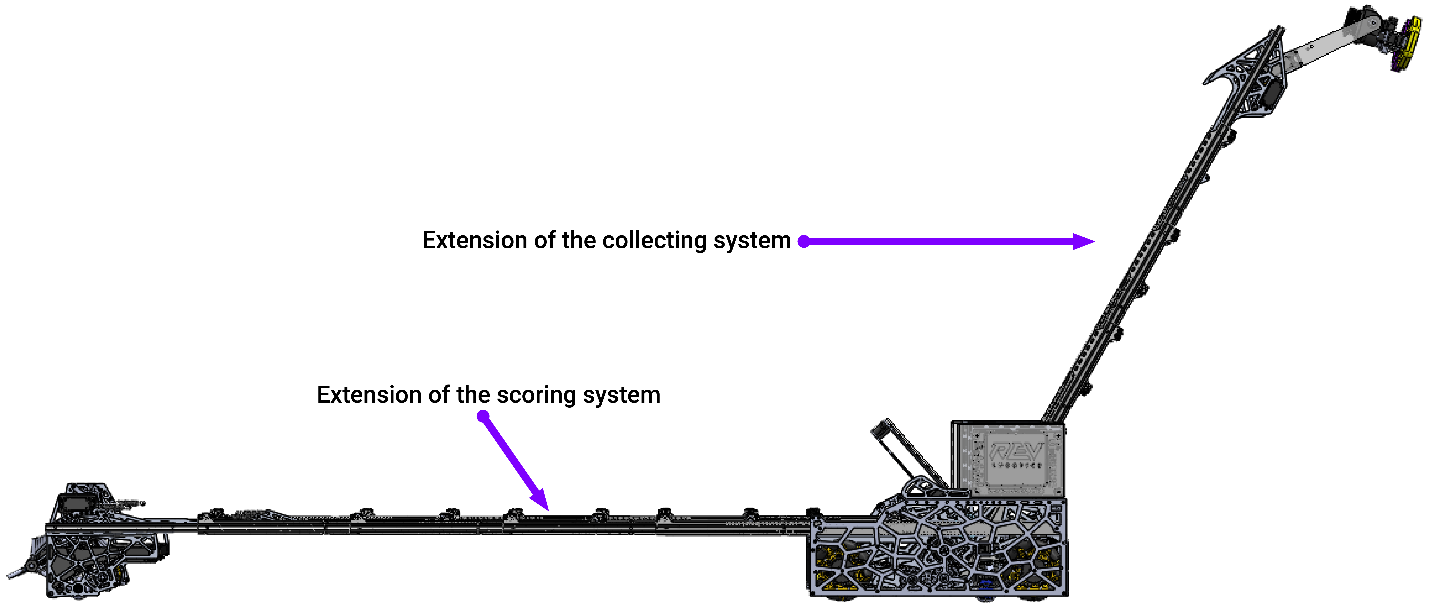
Our robot uses a double linear extension for both intake and outtake system. We have implemented a PTO for the hanging system in order to minimize the mass of the robot. Due to the use of analog and digital sensors, we have implemented a list of fail safes in the autonomous period, but we also used them in teleOP.
DLS V1 - POWER PLAY 2022-2023
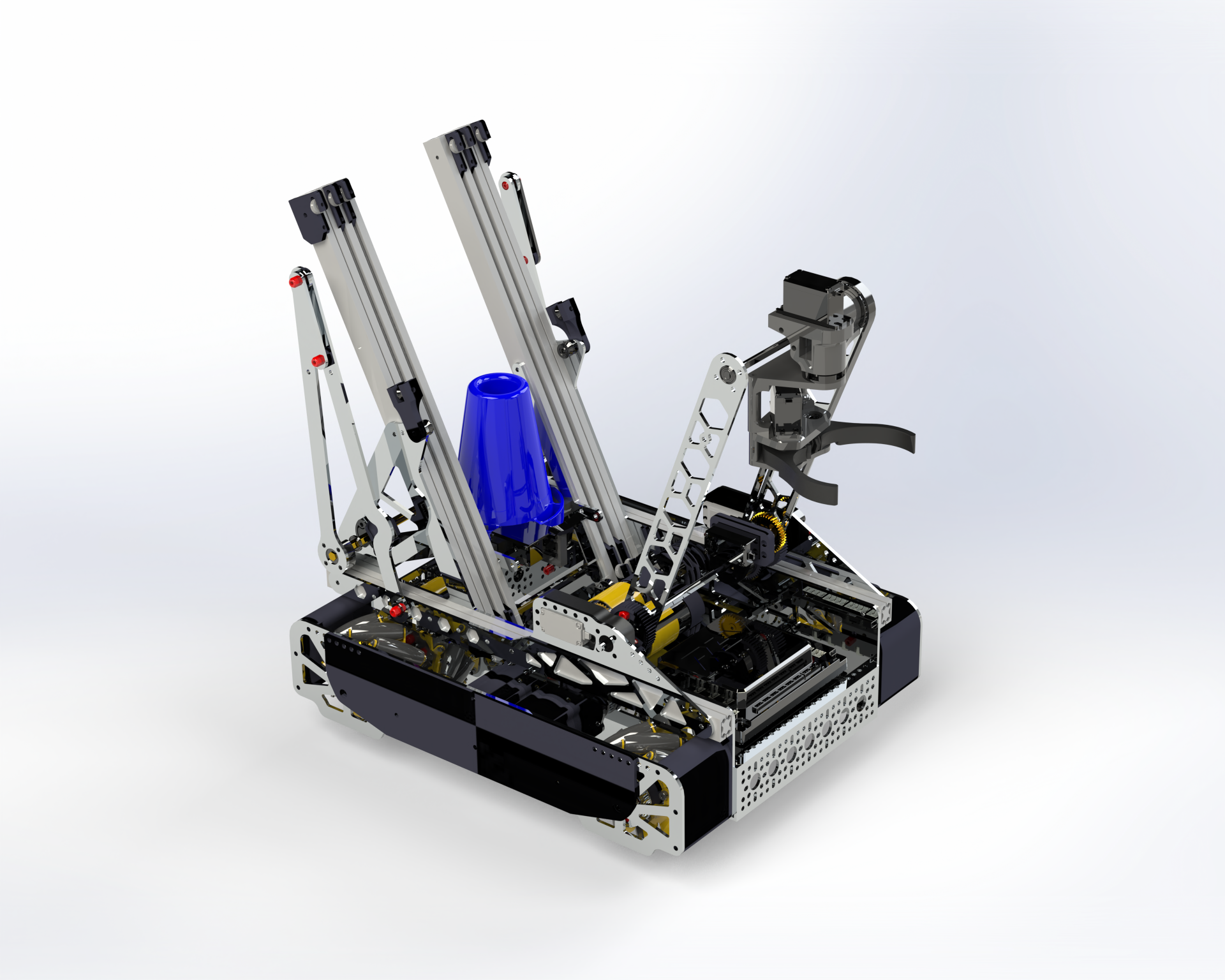
In approaching each design of our systems, we strictly follow an iterative engineering process that maximizes the chances of success by abstracting and analyzing weaknesses in detail in the virtual environment before prototyping. This strategy allows our team to consider many potential solutions for the season's mission without increasing the cost and production time. Thus, we were able to use more than 90% custom-made parts for our robots during the Power Play season, allowing for greater creative freedom in our designs.
Through the advanced use of Solidworks Computer Aided Design software, the use of 4 3D printers and a CNC to manufacture the custom parts, the virtual simulation of the forces exerted on the systems, and the collaboration with university physics professors for the theoretical calculation of the efficiency and feasibility of the designs, the team managed to build two robots with the highest competitive aptitudes.
Extensive planning and research allowed us to arrive at reliable solutions for our robots while seeking low system complexity to eliminate the risk of failure during matches. Thus, our goal is to achieve noticeable performance in the field game, being the winning alliance captains and inspiring award winners at the regional competition and the semifinalist alliance captain and inspiring award winners at the national competition, qualifying us for the world championship.
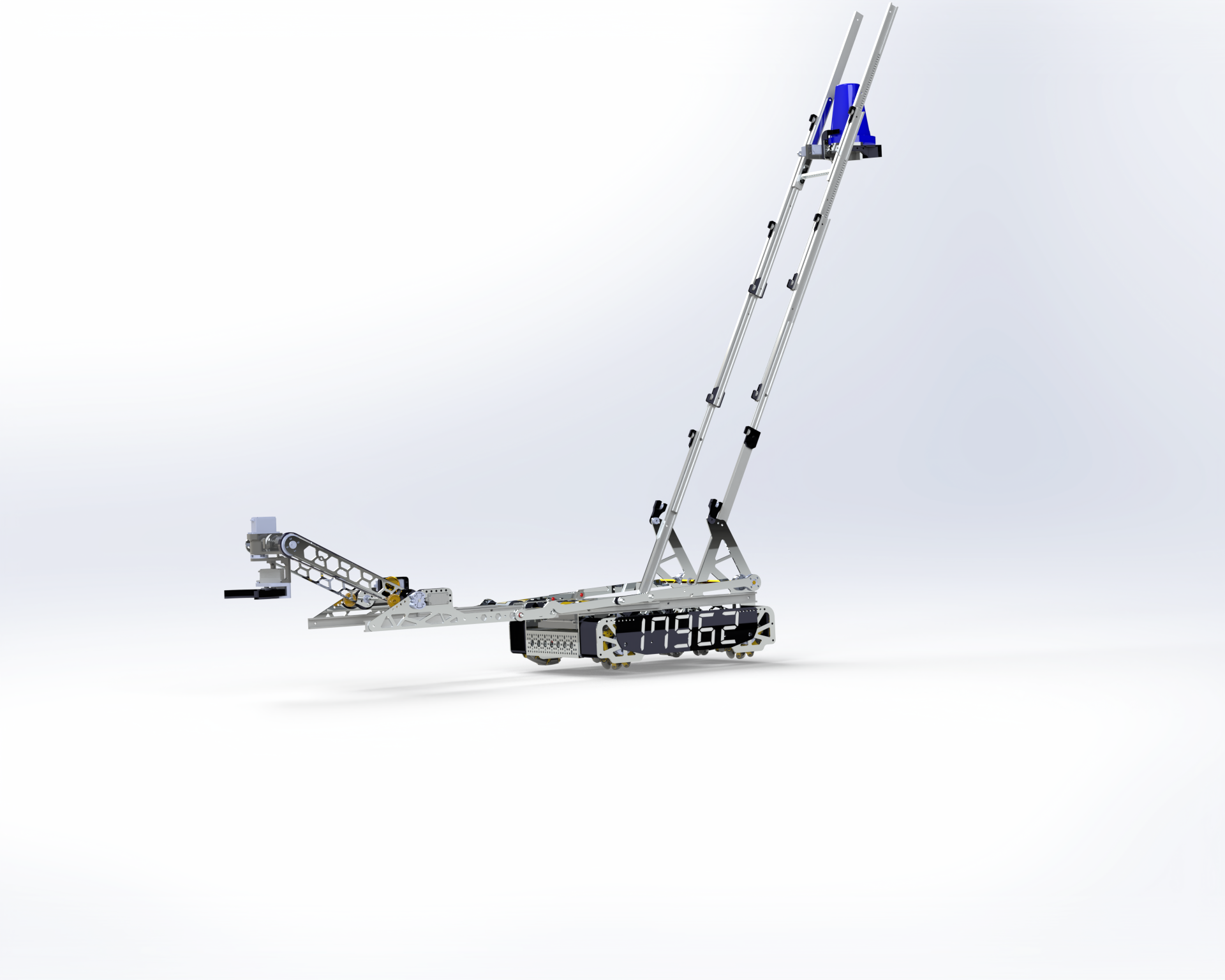
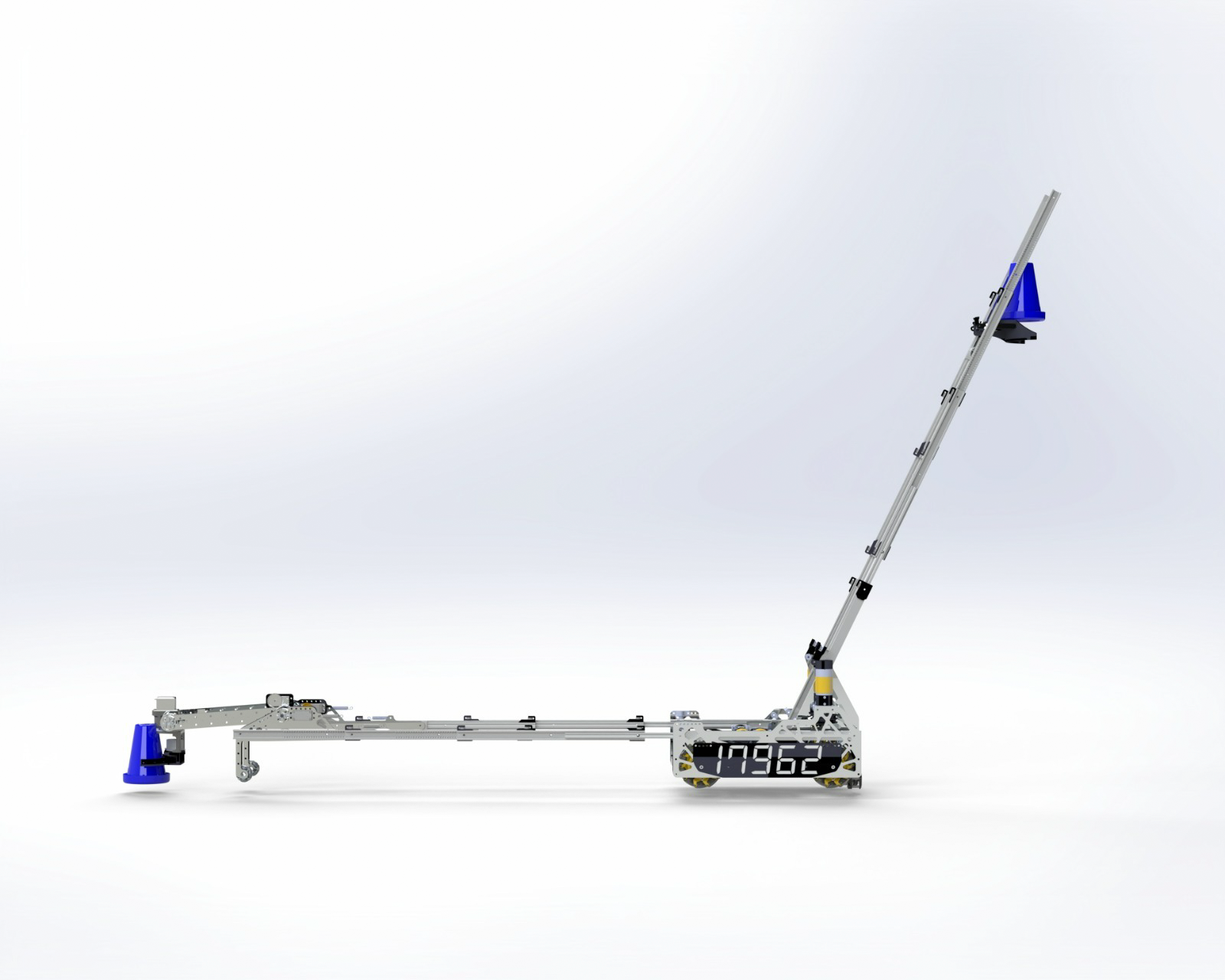